HET WALSPLATEREN VAN DUNNE METAALSTRIP
Diverse connectoren t.b.v. de elektronica bestaan meestal uit verschillende metalen die laagsgewijs zijn opgebouwd. Dergelijke componenten worden meestal gestanst uit een gecladde strip die veelal op rol c.q. coil wordt aangeleverd. Het is dan van groot belang dat deze samengestelde metaalstrippen een zogenaamde metaalbinding bezitten om geen onnodige elektrische verliezen te krijgen. Dit houdt in dat elektronen vrijelijk van het ene metaal naar het andere kunnen bewegen zonder dat ze te maken krijgen met een overgangsweerstand.
Bekende methoden om kostbare metallische deklagen aan te brengen op een relatief goedkope drager worden o.a. gedaan met galvanische technieken. Dat neemt niet weg dat er ook andere processen mogelijk zijn en daarbij kan gedacht worden aan bijvoorbeeld opdampen en vooral aan walsplateren dat ook wel walsbekleden wordt genoemd. Laatstgenoemde methode blijkt qua kostprijs meestal het aantrekkelijkst te zijn en daarom wordt in deze blog daar voornamelijk aandacht aan besteed.
Onder kostbare metallische deklagen worden vooral de metalen goud, platina en zilver bedoeld en het hoeft verder geen betoog dat men er dan altijd naar streeft zo’n deklaag zo dun mogelijk te houden. Dergelijke metalen zijn onmisbaar in allerlei elektrische contacten t.b.v. de halfgeleidersector en een goed dagelijks voorbeeld is het gebruik van deze metalen in mobiele telefoons en computers Met walsplateren kan men naast strip ook microprofielen en beklede draad vervaardigen. Voor het dragermateriaal gebruikt men meestal koper- en nikkellegeringen en commercieel zuiver aluminium. Ook metalen als hardbaar verenstaal, ijzernikkellegeringen, laag en hoog gelegeerd staal alsmede roestvast staal worden soms als dragermetaal toegepast.
Er zijn twee verschillende methoden om met walsplateren deze samengestelde producten te vervaardigen. Dat betreft het plaatplateren, dat ook wel blok- of warmperslassen wordt genoemd en het walsplateren zelf. Bij het plaatplateren worden ingelegde metalen aangebracht in groeven die gefreesd worden in het dragermateriaal. Door druk en verhoogde temperatuur worden de twee metalen aan elkaar verbonden waarna het door diverse walsingen op de gewenste dikte wordt gebracht. Er moet meestal tussen de walsingen door rekristalliserend gegloeid te worden. Nadelen zijn dat men over het algemeen relatief korte staven verkrijgt met verhoudingsgewijs veel inlegmateriaal. Daarom wordt deze optie vanwege de relatief hoge kostprijs niet veel gebruikt. De meest voorkomende methode is het walsplateren dat schematisch is weergegeven in afbeelding 1.
Alle genoemde nadelen van het plaatplateren zijn met deze techniek verdwenen. Walsplateren is een continue kouddruklasproces dat de drager en toplaag metallisch verbindt terwijl een reductie van meer dan 50% op de materiaaldikte ontstaat. Vaak wordt bij zeer kostbare metalen ook nog een tussenlaag aangebracht van zuiver nikkel die de binding verder optimaliseert. Bovendien fungeert dit nikkel als een barrièrelaag die voorkomt dat atomen van het ene metaal naar het andere metaal migreren. Ook hier geldt dat er de nodige gloeiprocessen nodig zijn om tot een optimaal eindresultaat te komen. Het eindproduct wordt opgerold tot een coil waardoor a.h.w. een eindeloze strip ontstaat wat ten goede komt aan het rendement van het stansproces. Het walsproces is dusdanig veredeld dat de fysische en technische parameters van de strip onder zeer nauwkeurige toleranties zoveel mogelijk constant blijven.
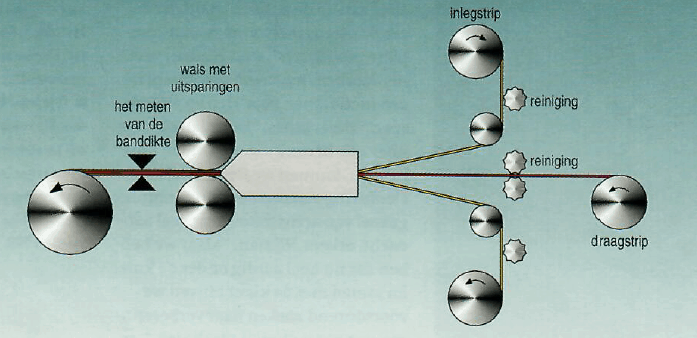
De inlegmetalen zijn onder te verdelen in drie groepen t.w. edelmetalen zoals goud, zilver, platina en hun legeringen t.b.v. hoogwaardig contactmateriaal in de elektronica. Daarnaast koper en nikkel als soldeermateriaal t.b.v. slecht soldeerbare metalen zoals aluminium en aluminiumlegeringen. Tenslotte tin en legeringen van lood/tin die gebruikt worden voor allerlei componenten in de elektrotechniek. Walsbeklede stroken kunnen zowel aan een zijde of aan beide zijden worden aangebracht. Dat kan ook partieel gebeuren zoals te zien is op afbeelding 2.
De strookdikten variëren in de praktijk tussen 0,04 en 2,5 mm en een standaarddikte is veelal 1,5 mm. De strookbreedte is maximaal 250 mm en de toleranties voor de afmetingen staan vermeld in de norm DIN 1777. De minimale dikte van de platering is 0,8µm maar m.b.v. bepaalde technieken en voor een beperkt aantal metalen kan men zelfs tot nog dunnere afmetingen komen en wel tot slechts 0,2µm. Tijdens het maken van coils wordt zacht papier mee gewikkeld om beschadigingen te voorkomen. Walsbeklede strippen laten zich gemakkelijk snijden, stansen, buigen en dieptrekken. Vanwege de walstextuur is de buigbaarheid van het materiaal op de walsrichting beter dan evenwijdig aan de walsrichting en dat is vooral relevant indien men scherpe buighoeken van 90° moet maken.
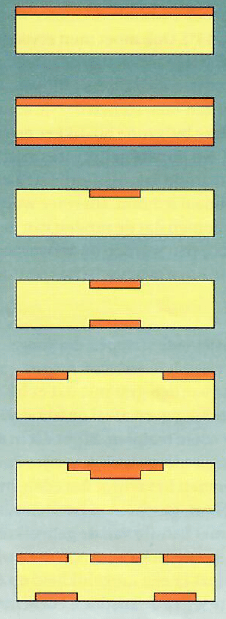
Heeft u nog vragen over het toepassen van bepaalde RVS kwaliteiten of andere legeringen?
Metaalselector is een computerprogramma dat in eigen beheer ontwikkeld is om een juiste keuze te maken op basis van corrosie- en materiaal eigenschappen.
Ga naar Metaalselector.nl voor meer informatie en om eigen toegang te krijgen tot dit programma, waarmee u een eigen gedegen materiaalkeuze kunt maken voor uw toepassingen.
Vind hier ook mijn blogs welke geschreven zijn voor AluRVS: https://www.alurvs.nl/roestvast-staal/Blog/
en AluRVS Staal: https://www.alurvs.nl/staal/blog/