NIEUWE KANSEN DANKZIJ EXPLOSIEVE METAALBEWERKING
Dat men met explosieven iets kan opblazen of vernietigen is een ieder wel bekend. Dat noemt men ook wel demolitie of destructie. Wat veel minder mensen weten is dat men met explosieven ook constructieve dingen kan doen en dat met name met metalen. Voorbeelden hiervan zijn explosief lassen, bekleden, vormen en snijden. In deze blog houden we ons beperkt tot het lassen en bekleden van metalen. Daarom volgt nu een beknopte uiteenzetting.
Als twee of meerdere metalen d.m.v. explosieven op een gecontroleerde wijze tegen elkaar worden geschoten, ontstaat er een metallische lasverbinding die over een hoge kwaliteit beschikt. Deze vorm van lassen is een variant van het zogenaamde kouddruklasproces. Dankzij afstandhouders worden de te lassen platen op een bepaalde afstand van elkaar gebracht. Daarna wordt op de bovenste plaat in een aangebracht frame een explosief poeder aangebracht met een detonator. Tijdens de explosie wordt de bovenste plaat met een enorme snelheid tegen de onderplaat geschoten waardoor de atomen een atomaire metaalbinding zullen vormen. Voordat deze binding tot stand komt, moeten eerst alle oxiden verwijderd zijn. Hoewel men van te voren zoveel mogelijk roest van het staal mechanisch heeft verwijderd, ontstaat er meestal weer een dun oxidehuidje dat tijdens het lasproces automatisch wordt verwijderd. Dat geldt vooral voor metalen die van zichzelf een metaaloxidehuid hebben zoals roestvast staal, titaan en aluminium.
Dankzij de schokgolven en de extreem hoge druk ontstaat er op het botsingspunt van de twee metalen een superplasticiteit die dit schokgolfpatroon laat aftekenen. Tijdens het formeren van dit golfpatroon breekt de oxidehuid los van de ondergrond en door de zogenaamde jetvorming wordt deze materiestroom van oxiden en verontreinigingen voor het detonatiefront uitgedreven. Dat de oxidehuid los komt van de matrix kan men enigszins vergelijken met het uitkloppen van een deurmat. Doordat de schokgolf in extreem korte tijd de superplastische interface laat golven wordt de oxidehuid gebroken en losgerukt van het metaaloppervlak. Schematisch kan men dat in onderstaande afbeelding zien.
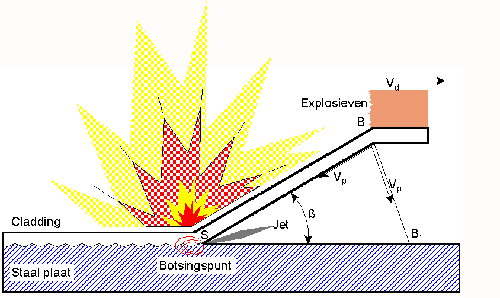
Na dit verwijderen vindt pas het echte lasproces plaats. De druk is nog steeds zo groot dat de atomen van de oxidevrije oppervlakken in elkaars beïnvloedingssfeer komen waardoor er per definitie een metaalbinding ontstaat. Dit kan verklaart worden door de veranderende loop van de valentie-elektronen in de buitenschil schil van het atoom dat nu eenmaal geen sterke binding heeft met de kern. Op deze wijze kan dit elektron gemakkelijk in een baan komen van een ander atoom waardoor de binding een feit is.
Deze vorm van lassen is mogelijk tussen de meest voorkomende metalen. Dit proces kan in de open lucht worden uitgevoerd alhoewel de beste resultaten worden bereikt in een vacuüm conditie. Explosief lassen in niet te mechaniseren of te automatiseren en het is per definitie ook geen handlasproces. De temperatuur van de metalen neemt tijdens dit lasproces nauwelijks toe.
Zoals reeds is gesteld kunnen de meest voorkomende metaalcombinaties op deze wijze aan elkaar worden gelast. T.a.v. de materiaaldikten kan gesteld worden dat het substraat onbeperkt dik mag zijn terwijl aan de cladding c.q. 'flyer' beperkingen zijn opgelegd. Dit is in feite ook de bedoeling omdat dit proces veelal juist bedoeld is om kostbaar metaal uit te sparen. Het zal dan duidelijk zijn dat men het te cladden kostbare metaal zo dun mogelijk wil houden. Naast bekledingen kan men dit proces ook toepassen om pijpen in pijpplaten te lassen, nozzles inwendig te bekleden, enz.
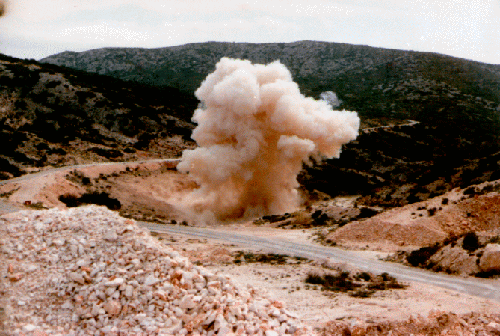
TOEPASSINGEN
De meeste toepassingen vindt men terug in de apparatenbouw zoals pijpenplaten, bodems, wanden van reactorvaten e.d. Alles is er dan op gericht om de mechanische sterkte van het stalen substraat te genieten en de corrosiebestendigheid van een dun hoogwaardig metaal. Dat betreffen veelal roestvast staal, nikkellegeringen, titaan en zirkoon. Onderzoek heeft uitgewezen dat de verbindingen hoogwaardiger worden indien dit unieke lasproces in een vacuümconditie plaatsvindt.
Indien het zwaartepunt van een nieuw te bouwen schip te hoog gaat uitvallen, dient men de opbouw van het veel lichtere aluminium te maken. Hiermee voorkomt men dat een schip instabiel wordt en tevens bespaart men brandstof omdat er veel minder massa verplaatst hoeft te worden. Dit levert gelijk een probleem op omdat aluminium niet aan staal te lassen is met bestaande thermische lasprocessen. Daarom is een product ontwikkeld m.b.v. het explosieve lasproces om het verbinden met thermisch lassen toch mogelijk te maken. Dat is de reden dat de scheepsbouw gebruik maakt van zogenaamde transition joints c.q. verbindingsstrippen die ook wel Triplate worden genoemd. Zie www.triplate.com
Triplate bestaat uit drie lagen metaal, namelijk koolstofstaal 52-3N als basismateriaal, commercieel zuiver aluminium 99,5 (Alloy 1050A) als overgangslaag en het corrosiebestendige AlMg4,5Mn (Alloy 5083) als bovenlaag. De staalzijde van Triplate wordt aan het stalen dek gelast en de aluminium opbouw aan de bovenkant van deze verbindingstrip.
Neem contact op met Innomet b.v. voor meer informatie over explosief lassen en Triplate.
Heeft u nog vragen over het toepassen van bepaalde RVS kwaliteiten of andere legeringen?
Metaalselector is een computerprogramma dat in eigen beheer ontwikkeld is om een juiste keuze te maken op basis van corrosie- en materiaal eigenschappen.
Ga naar Metaalselector.nl voor meer informatie en om eigen toegang te krijgen tot dit programma, waarmee u een eigen gedegen materiaalkeuze kunt maken voor uw toepassingen.
Vind hier ook mijn blogs welke geschreven zijn voor AluRVS: https://www.alurvs.nl/roestvast-staal/Blog/
en AluRVS Staal: https://www.alurvs.nl/staal/blog/