OPPERVLAKTEBEHANDELING VAN TITAAN (DEEL 2)
In het algemeen kan men stellen dat oppervlaktebehandelingen van metalen het doel hebben om de slijtvastheid te vergroten, de wrijvingsweerstand te verlagen en om aan bepaalde esthetische eisen te kunnen voldoen. Per definitie levert een oppervlaktebehandeling een verandering van de eigenschappen van dit oppervlak op. In dit opzicht verschilt de doelstelling van een oppervlaktebehandeling niet als we aan het metaal titaan denken. Het oppervlak van titaan kan zowel mechanisch, metallurgisch als chemisch veranderd worden. Bovendien kan men m.b.v. bepaalde coatingtechnieken een laagje aan het oppervlak bewerkstelligen die bijvoorbeeld de slijtbestendigheid en de wrijvingseigenschappen verbetert. Wat alle technieken gemeen hebben is het feit dat het basismateriaal geen nadelige invloeden zal ondervinden. Om de slijtbestendigheid te verhogen zijn er meerdere mogelijkheden die allemaal hun eigen kenmerken en kostprijs hebben. De uiteindelijke keuze van deze behandeling is sterk afhankelijk van het soort slijtage dat kan gaan optreden. Deze beschouwing geeft meer duidelijkheid over de variabelen. Klik hier voor Deel 1
Harden m.b.v. een zoutbad
Oppervlaktebehandelingen in verschillende zoutbaden bij temperaturen rond de 800°C geven een verhoging van de hardheid tot wel 800 HV dankzij interstitiële oxides, carbiden en nitriden die tot een dikte van 0,04 mm aanwezig zijn. In de tabel ziet men de dikte van de slijtlaag die men met de verschillende methoden kan verkrijgen en die nodig is voor een afdoende slijtweerstand.
Het nitreren van titaan
Er zijn verschillende processen commercieel beschikbaar die een zeer dunne en harde genitreerde laag bewerkstelligen op het titaanoppervlak. Deze laag is in de regel goudkleurig en slechts 4 micron dik. Titaannitride (TiN) is inert, biocompatibel (dus implanteerbaar) en kan toegepast worden tot een temperatuur van 480°C. Tegenover andere genitreerde oppervlakken is de wrijvingscoëfficiënt 0,05-0,15. Het plasma-nitreren is een eenvoudig en veelgebruikt proces omdat daarmee goede uniforme slijtlagen aangebracht (beter gezegd ingebracht) kunnen worden op alle denkbare vormen. Dit proces speelt zich af op een temperatuur van 700°C waardoor men ook rekening moet houden dat het materiaal hierdoor a.h.w. warmtebehandeld wordt. Men dient daarom echter ook rekening te houden met nadelen van deze behandeling omdat ook het oppervlak ruwer wordt en er treedt vaak een vermindering van de vermoeiingseigenschappen op. Dit laatste is vooral het geval bij dikkere genitreerde laagdiktes. Bij deze temperatuur wordt de titaanoxidehuid verwijderd zodat stikstof het oppervlak binnen kan diffunderen met een harder substraat als gevolg waar uiteindelijk het slijtvaste titaannitride op aangebracht kan worden. Men kan dit proces ook af laten spelen bij een temperatuur van 450°C, waardoor er geen oppervlakteverruwing optreedt.
De laag die dan ontstaat is echter dunner (3 microns) en heeft een veel slechtere hechting op het onderliggende titaan. Bij grote belastingen kan zo’n laag dan ook snel beschadigd worden. Daarom kan men dit substraat het beste eerst verstevigen en versterken m.b.v. lasersmelting met stikstof. Men noemt dit proces ook wel laser-nitreren. Ook kan dit versterken en verstevigen bereikt worden door bepaalde legeringsadditieven aan te brengen in het oppervlak m.b.v. het elektronenstraalsmelten. Ruwweg kan men stellen dat een vertienvoudiging van de geharde laag een verdubbeling geeft van de slijtbestendigheid waardoor de prestaties van titaan min of meer vergelijkbaar zijn met dat van gehard staal. Genitreerde titaanassen van 4 meter lang die gebruikt zijn in het Snorre Leg Platform in Noorwegen hebben een laagdikte van 5-12 microns met een gemiddelde hardheid van 900 HV. Ook de motorrace is een grote gebruiker van genitreerde titaancomponenten. We kunnen hierbij denken aan onderdelen in afsluiters en klepinrichtingen, doch ook verbindingsassen, lagers, naven en andere slijtdelen. Ook worden genitreerde kogels in afsluiters met succes toegepast in de maritieme en chemische industrie. Genitreerde onderdelen die in het lichaam worden geïmplanteerd dienen eerst gepolijst te worden i.v.m. het ruwere oppervlak. Een van de grootste problemen die men met het nitreren tegenkomt is de verlaging van de vermoeiingssterkte als gevolg van kleine microscheurtjes in het genitreerde oppervlak die zich in het moedermateriaal kunnen ‘voortplanten’. Dit probleem versterkt zich naarmate de laagdikte toeneemt.
Soort proces | Laagdikte in microns |
---|---|
zuur anodiseren + smeermiddel | 0,1 |
diffusie van stikstofionen | 0,5 |
ioniserend plateren/zachte metalen | 1 |
nitreren | 6 |
alkalisch anodiseren + smeermiddel | 7 |
plasma nitreren | 30 |
gesmolten cyaanzout | 60 |
thermische gasdiffusie | 70 |
elektroplateren met hardmetaal | 80 |
chemisch vernikkelen | 90 |
elektroplateren zachte metalen | 110 |
thermisch sprayen van een coating | 300 |
thermisch sprayen van zachte metalen | 500 |
legeren van het oppervlak met een laser | 700 |
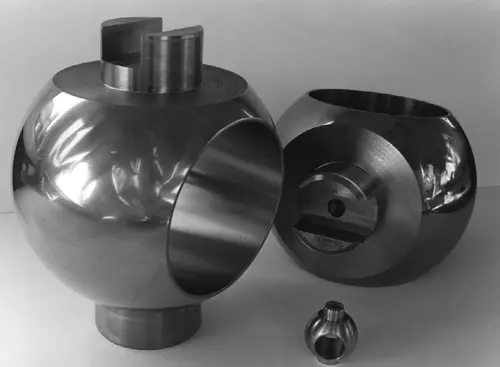
Metallische coatings
Omdat titaan een oxidehuid heeft, moet het materiaal voorbehandeld worden voordat men overgaat tot het plateren. Deze oxidehuid vormt een barricade om een goede hechting te krijgen van de platering en dient dus daarom verwijderd te worden m.b.v. diverse behandelingen waaronder etsen en andere oppervlakteactivaties.
Galvanisch plateren
Een van de meest gebruikte methoden is het galvanisch plateren met chroom dat ook wel hardverchromen wordt genoemd. De laagdikte varieert tussen 5 en 250 micron en de hardheid is 900-1050 HV. Toepassingen treft men vooral in dragende componenten t.b.v. de luchtvaart, actuatoren, automobielindustrie zoals zuigers, klepveren, dragende delen voor nokken- en krukassen. Teneinde de vermoeiingseigenschappen te behouden wordt vooraf het component onderworpen aan een shot-peeningbehandeling. Dit geldt overigens niet voor dunne voorwerpen. Bij zeer zware deklagen kan het soms noodzakelijk zijn dat er nog enige mechanische nabewerking nodig is om de juiste afmetingen te krijgen. Hardverchromen heeft een negatieve invloed op de vermoeiingssterkte van het titaan, doch dankzij een shot-peening, mogelijk gecombineerd met een warmtebehandeling, geeft het toch weer goede resultaten. Het invreten van titaan kan men het beste bestrijden met metallische deklagen die bestand zijn tegen oxiderende invloeden zoals men bijvoorbeeld krijgt met het chemisch vernikkelen of met nog zachtere, zelfsmerende deklagen zoals zilver, indium, koper en tin. Koper geeft de beste resultaten van alle zachte metallische deklagen als het om het invreten en vermoeiing gaat. Als men een deklaag van 50 micron koper aanbrengt na het shot-peenen, dan bewerkt dat een toename in de weerstand tegen het vreten van maar liefst 150%. In het verleden gebruikte men ook wel cadmium, doch dat leidde tot verbrossing en spanningscorrosie en wordt daarom afgeraden. Dit is zeker het geval bij het gebruik van kritische onderdelen zoals bouten en moeren.
Chemisch plateren
Chemisch plateren gebeurt zonder een stroombron en het grote voordeel van dit proces is de zeer egale dikte van de deklaag. Op deze wijze kan men zelfs componenten bewust onder de maat produceren waardoor deze dankzij dit proces zeer nauwkeurig aan de maat kunnen komen. Een nikkelplatering op titaan kan dankzij een warmtebehandeling van 1 uur op 400°C qua hardheid toenemen van 450-650 HV tot 950-1050 HV. Deze warmtebehandeling heeft geen invloed op de karakteristieken van het ongelegeerde titaan, doch kan mogelijk wel wat effect hebben op de eigenschappen van titaanbètalegeringen die onderworpen zijn geweest aan een verouderingswarmtebehandeling.
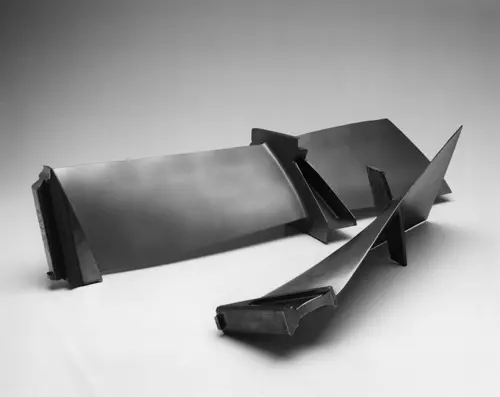
Dankzij een opgespoten coating van wolfraamcarbide (0,25 mm dik) werd het invreeteffect op deze titaanschoepen vertraagd van 100 uur naar 30.000 uren. Het slijteffect op de basis van deze schoepen werd nagenoeg geheel opgeheven door een galvanisch opgebrachte koper-nikkel-indium laag.
Bron: Courtesy Praxair Surface Technologies Ltd. en Timet UK.
Plateren met ingebedde bestanddelen
Zowel bij het galvanisch als het chemisch plateren kan men kleine harde of smerende bestanddelen laten inbedden in de slijtlaag, zoals bijvoorbeeld nikkelborium of een PTFE (polytretrafluoroethyl)-coating. De metallische deklaag zorgt dan voor de samenbinding. Het nikkelborium geeft een zeer goede slijtbestendigheid en heeft een lage wrijvingscoëfficiënt; het kan toegepast worden tot 500°C. Het PTFE fungeert als een zacht droog smeermiddel. Bij het chemisch plateren met nikkel gevolgd door een warmtebehandeling bij 300°C gedurende 4 uur heeft men dan een hardheid van ongeveer 400 HV verkregen. Toepassingen zijn mogelijk tot een temperatuur van maximaal 300°C.
Thermisch sprayen met metalen en keramiek
Er zijn diverse thermische-spraysystemen ontwikkeld, zoals het plasma-sprayen, HVOF (high velocity oxy-fuel)
en het vacuüm plasmaproces. Vele keramische en carbidehoudende deklagen, doch ook metalen en metaallegeringen, kunnen m.b.v. het HVOF- en plasmasprayproces met succes worden aangebracht. Het doel is om de prestaties te verbeteren van bijvoorbeeld de vreetneigingen, slijtbestendigheid, elektrische isolatie, erosieweerstand e.d. Poreuze deklagen kunnen de slijtbestendigheid verder vergroten omdat de poriën smeermiddelen absorberen. Spraydeklagen die m.b.v een hydroxielapatietvlam zijn aangebracht worden meestal alleen gebruikt voor implantaten waardoor het samengroeien met het botweefsel wordt gestimuleerd.
Zachte metalen zoals koper, koper/nikkellegeringen, indium en aluminiumbrons zijn prima metalen teneinde de
vreetneigingen te verlagen en de glij-eigenschappen te verbeteren. Met thermisch sprayen verkrijgt men een zeer goede binding met het titaansubstraat. Dit proces wordt gedaan door gespecialiseerde bedrijven die ook voor de juiste voor- en nabehandeling zorgen.
Verfdeklagen en polymeercoatings
Verfsystemen
Omdat titaan een uitzonderlijke corrosiebestendigheid geniet, wordt het maar zeer zelden voorzien van een verfsysteem. Heel soms kan een verfsysteem aangebracht worden indien er absoluut geen vonken worden getolereerd of ook wel om redenen die te maken hebben met camouflage, esthetica of identificatie. De voorbehandeling van het titaan wordt normaal gesproken door de verffabrikant opgegeven, doch meestal is dat goed ontvetten, beitsen of een glasparelbehandeling. Ook hier geldt dat shot-peening de voorkeur heeft, omdat naast de uitstekende binding van de coating ook nog een verbetering optreedt van de vermoeiingseigenschappen.
Polymeercoatings
Diverse toepassingen vereisen in combinatie met het gebruik van titaan een polymeercoating. Voor het bekleden van beton met titaanplaten in een ontzwavelingsplant is een fluoropolymeer coating ontwikkeld die als een bitumineuze bedding lokaal op het titaan is aangebracht i.v.m. het natte zure agressieve gas. Men moet uiterst kritisch zijn met de keuze van de coating omdat in bepaalde gevallen actieve fluoriden met het titaan kunnen reageren tijdens het aanbrengen en soms zelfs tijdens het gebruik. Een polyurethaancoating is wel eens gebruikt op titaanpijpen t.b.v. de offshore om galvanische corrosie te bestrijden die had kunnen optreden bij minder edele metalen die in contact stonden met het titaan. Ondanks de zeer goede erosiebestendigheid van titaan zijn er omstandigheden waarbij het titaan onacceptabele schade aan het oppervlak zou kunnen krijgen vanwege de combinatie inslagkracht en abrasiviteit van bepaalde harde deeltjes. Op deze wijze kunnen kleine kerfjes ontstaan die de vermoeiingssterkte aanzienlijk doen afnemen. Daarom heeft men bijvoorbeeld de binnenkant van de titaanstijgbuis in het Noorse Heidrun-project beschermd met HNBR-rubber (Hydrogenated Acrylonitrile Butadieen Rubber).
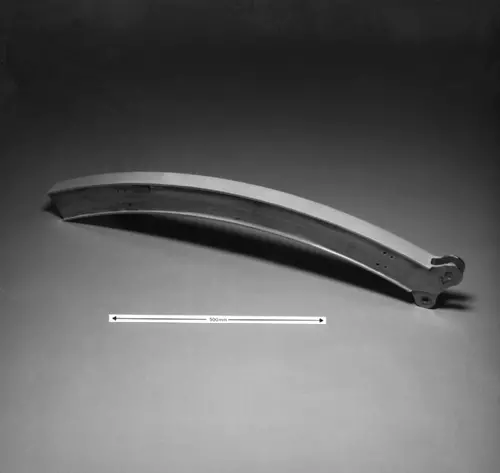
Titaan onderdeel van een vleugelklep van een Lockheed Tristar vliegtuig in de kwaliteit Ti-6Al-4V. Nadat deze ‘flaptrack’ was gerepareerd m.b.v. oplassen is deze gesprayed met een kobaltpoeder (87%), waardoor er een slijtlaag van 200 - 300 micron ontstond. Bron: Courtesy TWI, Marshall Aerospace en Timet UK.
Oppervlaktebehandeling voor speciale toepassingen
Diverse bekledingstechnieken zijn er voor titaan door de jaren ontwikkeld die het materiaal nog meer geschikt maken voor bepaalde toepassingen. Dit zijn veelal technieken die alleen maar door speciale bedrijven kunnen worden aangebracht. In het kort worden onderstaande systemen behandeld. Het cladden met andere metalen Titaan kan zowel met wals- als met explosiefplateren worden verbonden aan de meeste andere metalen. Voor het explosief plateren zijn in principe alleen die kwaliteiten geschikt die een lage of middelgrote mechanische sterkte bezitten zoals de typen grade 1, 2, 7, 11 en 12. Kwaliteiten met een hogere mechanische sterkte kunnen echter ook wel explosief worden aangebracht, doch dan moet men wel een tussenlaag van een lage sterkte toepassen. De bindingssterkte van de explosieve verbinding is doorgaans altijd hoger dan die van het walsplateren. Soms dient men ook rekening te houden met mogelijke galvanische corrosie in combinatie met metalen die lager in de spanningsreeks zitten en dat vooral bij natte agressieve corrosieve omgevingen. De meeste harde slijtbestendige legeringen zoals bijvoorbeeld stelliet hebben echter ook goede en soms zelfs betere corrosieprestaties dan titaan, waardoor dit probleem weer verdwijnt. Ook titaan dat gecombineerd wordt met metalen die min of meer op gelijke hoogte in de spanningsreeks staan zoals duplex, superduplex, *Hastelloy® en Inconel 625®, kan probleemloos toegepast worden in lichtreducerende, neutrale en oxiderende omstandigheden.
Het oplassen
Men kan harde of hardbare titaanlegeringen als een slijtlaag oplassen op zachtere kwaliteiten titaan. Dit kan ook partieel gebeuren op die plaatsen van een component waar men dit wenst. Een goed voorbeeld zijn de slijtringen in pompen en componenten waar voortdurend druppelinslag van water optreedt. Voor dit laatstgenoemd geval kan men uitstekend de hardbare molybdeenhoudende bètalegeringen gebruiken die een twintigvoudige levensduurverlenging geven t.o.v. commercieel zuiver titaan.
Elektrolytisch polijsten van titaan
Uiteraard kan titaan met de hand gepolijst worden, doch het nadeel is dat men geen constante oppervlaktegesteldheid kan verkrijgen. Bovendien is deze methode uiterst arbeidsintensief. Daarom kan men beter gebruikmaken van het elektrolytisch polijstproces omdat men dan zeer gecontroleerd de oppervlakteconditie kan bepalen. Er zijn echter niet veel bedrijven die een ruime ervaring hebben opgebouwd met het polijsten van titaan.
Verantwoording
De auteur is dank verschuldigd aan de Titanium Information Group en de National Surface Engineering
Centre in Engeland die beide voor relevante informatie hebben gezorgd.
*Hastelloy® en Inconel® zijn handelsmerken van respectievelijk Haynes International en Inco Family of Companies
Zie ook deel 1 van dit artikel.
[…] ook deel 2 van dit […]