WATERSTOFBROSHEID ALS GEVOLG VAN HET LASSEN
Indien men austenitisch roestvast staal gaat lassen met het TIG-lasproces dan is het inerte argon het best toepasbare schutgas omdat het gebruik hiervan leidt tot een zuiver smeltbad. Bovendien veroorzaakt argongas een hogere thermische inbreng. Echter aan elk voordeel kleeft een nadeel want men krijgt hierdoor een relatief lage lassnelheid en dat is uiteraard kostprijsverhogend.
Daarom wordt in de praktijk bij voorkeur 2 tot 5 % waterstof aan het argon toegevoegd want daardoor kan men de lassnelheid aanzienlijk verhogen. Toevoeging van waterstof aan argon bewerkt een hogere boogspanning. Dat betekent veelal een lasversnelling tot 30% in vergelijking met het lassen zonder waterstof. Dankzij waterstof wordt de vlamboog ook behoorlijk smaller waardoor de warmte op een geringer oppervlak geconcentreerd wordt. Ook doet men er goed aan een laminaire stroming van het gas na te streven en dat kan met een zogenaamde gaslens. Het effect hiervan is weergegeven in onderstaande afbeelding.
Dankzij waterstof ontstaat er door zo’n geconcentreerde lasboog een betere aanvloeiing van het smeltbad. Dat vereenvoudigt het lasproces en dat is zeer plezierig in het besef dat het steeds moeilijker wordt om goede vakkundige lassers te vinden. Als extra voordeel van de waterstofadditie is dat de lasnaad en de warmte beïnvloedde zone minder verkleurt door aanloopkleuren.
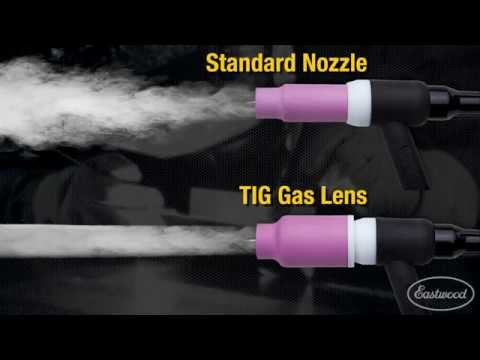
Ook tijdens het gebruik van formeergas maakt men graag gebruik van enige toevoeging van waterstof met als doel de eventueel aanwezige zuurstof te binden. Dit vindt plaats volgens de formule H2 + O2 → H2O. Op deze wijze wordt voorkomen dat mogelijk aanwezig restzuurstof een licht verbrand oppervlak bewerkstelligt van de doorlaszijde. Verkleuring zal uiteindelijk de corrosiebestendigheid ondermijnen dus dat moet zoveel mogelijk voorkomen worden. Veelal accepteert men een verkleuring die men kan omschrijven als strogeel.
Uit het bovenstaande blijkt de waardevolle bijdrage van de waterstoftoevoeging tijdens het lassen van roestvast staal maar er dreigt helaas ook een gevaar en dat is waterstofverbrossing.
Waterstofbrosheid is het gevolg van diffusie van waterstofatomen in het materiaal. Dit gediffundeerde waterstof kan in het materiaal lokale verbrossing veroorzaken. De ferritische structuur is echter veel gevoeliger voor waterstofverbrossing dan austeniet. Daarom is het belangrijk dat men maatregelen neemt om te voorkomen dat er waterstofopname via de lasboog in het lasmetaal komt. Dat geldt ook voor duplex roestvast staal omdat duplex immers voor de helft uit ferriet bestaat. Ook het gebruik van waterstofhoudend backinggas moet in dergelijke gevallen sterk worden afgeraden omdat dit ook aan de doorlaszijde waterstofbrosheid kan veroorzaken. Bij austenitisch roestvast staal ligt dit dus veel minder kritisch.
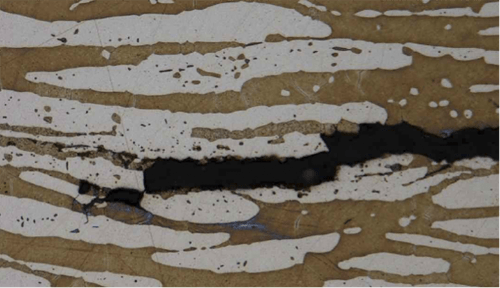
Waterstofverbrossing kan naast het lasproces ook het gevolg zijn van spanningscorrosie en dat betreft een bijzonder ernstig fenomeen. Een combinatie van mechanische spanning en een chloridenhoudend milieu bewerkt een versnelde corrosie op die plaatsen waar de spanning het hoogste is waardoor relatief snel scheurvorming optreedt terwijl het materiaal in de buurt nog volkomen gezond is. Het begint vooral op de bodem van scherpe kerfjes zodat bij verbrossing een scheur gemakkelijk en snel verder kan lopen met breuk tot gevolg. Heel soms lopen de scheuren langs de korrelgrenzen maar meestal gaan ze dwars door de kristallen heen. Dat noemt men respectievelijk interkristallijne en transkristallijne scheurvorming.
De reden dat de corrosie zich zo hevig focusseert op een spanningsgebied kan verklaard worden door het feit dat ten gevolge van de mechanische spanning scheurtjes in de oppervlaktehuid ontstaan waardoor er een potentiaalverschil komt tussen de veelal geoxideerde huid en het blanke metaal in de scheurtjes. Op deze wijze ontstaat er een relatief klein actief breukoppervlak tegenover een groot passief glad oppervlak. Bovendien krijgt men door de kerfwerking in de scheurtjes plaatselijk zeer hoge spanningen in het metaal waardoor de scheurvorming met rasse schreden zich kan voortplanten wat uiteindelijk breuk tot gevolg heeft. Tijdens de galvanische werking ontstaan er waterstofionen die gedeeltelijk het materiaal binnendringen (diffunderen) en dat zal in de regel weer verbrossing van bijvoorbeeld het roestvast staal opleveren waardoor de scheurvorming nog sneller verloopt. Ook speelt de omgevingstemperatuur een grote rol.
Vind hier ook mijn blogs welke geschreven zijn voor AluRVS: https://www.alurvs.nl/roestvast-staal/Blog/